resistances on the hull of the ship
The design of the hull of ships and boats is quite a challenging job because there are quite a number of variables that should be taken into account. One of the calculations that is quite important in hull design is resistance, because the magnitude of the resistance determines the effectiveness of the hull design that we make, more than that, the resistance will also affect the amount of engine power needed to move the ship. The first thing we need to understand in calculating this drag is the interaction of the hull with the propulsion system.
The ship’s propulsion system interacts with the ship’s hull and changes the flow pattern and resistance value of the ship itself. To facilitate the analysis of the drag on the hull, sometimes the propeller and hull analyzers are separated during laboratory testing, and even the rudder is sometimes separated during testing. The method that is currently developing is using a computer, namely the Computational Fluid dynamics (CFD) method. CFD method may be used for comprehensive analysis with the help of computer modeling.
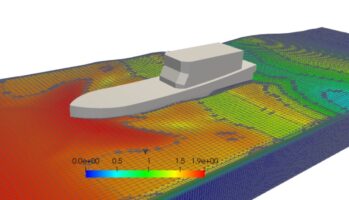
The calculation of the power required by the ship can be calculated using the general power equation:
POWER = FORCE * SPEED
Force is the drag or resistance of the ship and speed is the speed of the ship itself. From the above equation it can be shown that the resistance of the ship is directly proportional to the power required to move the ship.
The power required to push the ship forward is certainly less than the power generated by the thrust generated by the propeller, so the power generated by the propeller can be calculated using the following relationship:
THRUST POWER = THRUST * ADVANCE SPEED
Thrust is the force generated by the propeller that may the ship moving forward, while the advance speed is the velocity of the water flow before it reaches the propeller. On the propeller tested without the hull, this advance speed can be calculated easily based on the flow velocity. Meanwhile, in the presence of a hull, this velocity changes due to the interaction of the flow with the hull.
Thrust resulting from the propulsion test is higher than the hull resistance produced without a propeller, so calculations for additional resistance are needed with the following factors:
- The propeller adds flow velocity to the rear of the hull which increases frictional resistance.
- The propeller reduces the pressure on the back of the hull due to the high velocity (Bernoulli’s law).
The advance speed of the propeller is generally slower than the wake speed of the ship. The wake speed is divided into three components:
- Friction wake: due to viscosity, the relative speed of the vessel is slowed at the boundary layer, resulting in flow separation and resulting in a wake.
- Potential wake: Velocity at the stern is similar to that of the bow with a lower velocity at the stagnation point producing a wake flow.
- Wave wake: the wave system on the ship changes locally due to the orbital velocity below the wave, the wave fragment due to the propeller also increases the wake.
Wave wake is only significant for Froude number, Fn > 0.3. Wake on the towing tank test model is larger than the full scale boundary layer, then the flow separation is also relatively large and a correction factor is needed. The wake behind the ship without the propeller is called the nominal wake, while the wake behind the propeller is called the effective wake. The flow around the propeller accelerates the flow rate by about 5-20%.
Based on the above relationships, it can be calculated the ratio of effective power to thrust power which represents the efficiency of the hull design that we make, this parameter is also called hull efficiency which is mathematically written as follows:
HULL EFFICIENCY = EFFECTIVE POWER/THRUST POWER
= (RESISTANCE*HULL SPEED) / (THRUST*ADVANCE SPEED)
Then, based on the relationship between torque and rpm of the propeller, the power generated by the propeller can be calculated by the following equation:
POWER = 2.pi * RPM * TORQUE
Power at the above equation is less than the brake power, or the power generated by the propeller turning engine.
FACTORS CAUSED RESISTANCE ON THE HULL
After discussing the interaction between the hull and the propeller, then we will discuss the sources of ship resistance in general. In general, the causes of ship resistance are often separated into each category as follows:
1. Friction resistance: friction between the walls of the boat and the water causes a velocity difference between the speed on the wall of the boat and the speed of the water around the boat. The difference in velocity results in the emergence of a boundary layer that restrains the ship’s motion.
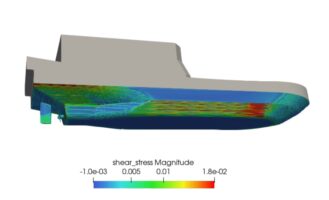
2. Viscous pressure resistance: the shape of the ship moving forward causes changes in the flow pattern around it, especially at the fore and aft. At the front there is stagnation pressure due to “stopping” the flow due to hitting the front of the ship, this pushes the ship with a force towards the rear. The wake at the rear of the ship produces an area of low pressure, this sucks the ship with a backward force. Ships with an elongated shape tend to have low resistance, but greater friction resistance, and vice versa.
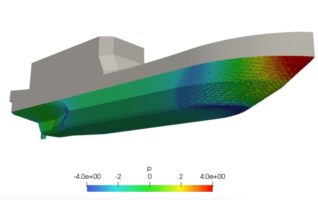
3. Wave resistance: the energy in the waves is generated by the motion of the ship which produces drag. This wave is divided into two primary and secondary waves.
(1) primary wave system: The flow at the fore and aft of the ship is lower than the middle, and the highest at the stagnation pressure at the fore. The pressure difference produces a primary wave pattern whose shape depends on the velocity, but the location of the maximum, minimum and zero height of the wave is not affected by the velocity. The wave height is directly proportional to the square of the velocity.
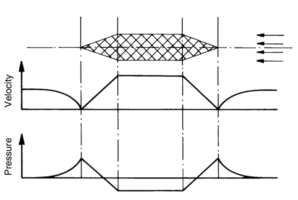
(2) Secondary wave system: On the free surface, waves are formed and flow towards the back of the ship. The wave pattern consists of transverse and divergent waves. In deep water, the wave forms an angle of 19.5 deg , the angle is not affected by the shape of the ship. In shallow water, the angle is 90 deg and gets smaller and smaller.
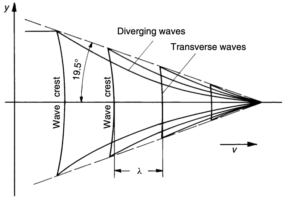
The design, especially the calculation of the resistance on the ship, is very complex if it is carried out using analytical calculations (pure mathematics), so experiments are needed to calculate it more easily, for example using a towing tank. However, the testing costs and time for prototyping are relatively high; so that the current design trend for ship hulls is to use computational fluid dynamics (CFD) using computational methods.
>>CLICK HERE FOR CFD SIMULATION ON SHIP HULL!

aeroengineering services is a service under CV. Markom with solutions especially CFD/FEA.
Leave a Reply
Want to join the discussion?Feel free to contribute!