material strength
Many materials of a structure are subjected to loads during use, such as the wings of airplanes and the shafts of automobiles. Under load conditions, it is necessary to know the characteristics of the material used so that the resulting deformation is not excessive and failure does not occur. The mechanical behavior of the material is a response to the applied load. The mechanical properties of the material can be determined by conducting tests taking into account the loading conditions, duration and environmental conditions which are arranged in such a way that they are close to their original conditions.
The mechanical behavior of the material can be determined by stress-strain testing, this test is often carried out for testing metals at room temperature. The test is carried out by applying a static load or a load that changes relatively slowly with time (quasi-static) on a cross section of the surface of the structural member. The results of these tests are engineering stress and engineering strain. Engineering stress (σ) is defined as the load (F) applied perpendicular to the cross-sectional area of the specimen (F/A0) with units of MPa or psi. Engineering strain (ε) is defined as the ratio between the increase in length due to loading (∆l) with the initial length of the specimen (l), engineering strain (ε) has no dimensions.
Material that is given a load will experience deformation, can experience elastic deformation or also plastic deformation. Elastic deformation is a non-permanent deformation which means that when the load is removed the material returns to its original shape, where the stress and strain are proportional to form a linear relationship. The gradient of the linear line is the modulus of elasticity (E). The modulus of elasticity is the stiffness property of the material or the resistance of the material to elastic deformation, the greater the modulus of elasticity the stiffer the material and vice versa. Plastic deformation is permanent deformation of the material, even when the load is removed. In plastic deformation, yielding phenomenon occurs, namely where there is a transition between elastic and plastic deformation. The measured stress when the yielding phenomenon occurs is called yield strength. After yielding occurs, the stress continues to increase to a maximum to continue plastic deformation. Tensile strength is the maximum stress that a material can withstand.
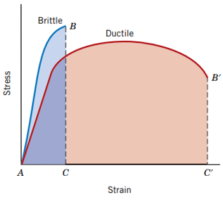
Ductility of a material is a material property that has the ability to undergo strain before fracture. Ductile materials usually undergo plastic deformation and reduction in cross-sectional area when fracture occurs and the necking phenomenon occurs. The fracture surface of the ductile material forms a cup and cone.
The brittleness of a material shows the properties of a material that does not undergo plastic deformation before fracture occurs. Brittle material breaks suddenly, does not experience strain, does not stretch before fracture and does not decrease in cross-sectional area before fracture. The fracture surface of a brittle material is usually flat.

Contributor: Feri Wijarnako
Leave a Reply
Want to join the discussion?Feel free to contribute!