Uji Tekan dan Puntir Pada Material Logam
Tentu saja, logam dapat mengalami deformasi plastis di bawah pengaruh yang diterapkan beban tekan, geser, dan torsi. Perilaku tegangan-regangan yang dihasilkan ke dalam daerah plastis mirip dengan pengaruh beban tarik. Namun untuk beban tekan tidak ada beban maksimal karena necking tidak terjadi dan mode patahnya berbeda dengan beban tarik.
Deformasi Tekan
Banyak operasi di bidang manufaktur, terutama proses seperti penempaan, rolling, dan ekstrusi dilakukan dengan benda kerja yang dikenai gaya tekan. Uji kompresi, di mana spesimen dikenai gaya tekan beban, memberikan informasi yang berguna untuk memperkirakan gaya dan kebutuhan daya dalam proses-proses ini. Tes ini biasanya dilakukan dengan mengompresi silinder padat spesimen antara dua pelat datar yang dilumasi dengan baik. Karena gesekan antara spesimen dan pelat, permukaan silinder spesimen menonjol, efeknya disebut barreling. Perhatikan bahwa spesimen ramping dapat tertekuk selama pengujian; dengan demikian, rasio tinggi-diameter dari spesimen silinder padat biasanya kurang dari 3:1.
Karena barelling, luas penampang spesimen berubah sepanjang tinggi, dan mendapatkan kurva tegangan-regangan dalam kompresi bisa sulit. Selanjutnya, gesekan menghilangkan energi, sehingga gaya tekan lebih tinggi dari itu sebaliknya memasok pekerjaan yang diperlukan untuk mengatasi gesekan. Dengan pelumasan yang efektif, gesekan dapat diminimalkan, dan luas penampang yang cukup konstan dapat dipertahankan selama pengujian.
Ketika hasil uji tekan dan tarik pada logam ulet dibandingkan, dapat dilihat bahwa kurva tegangan-regangan real bertepatan. Perilaku ini tidak berlaku untuk bahan rapuh, yang umumnya lebih kuat dan lebih ulet dalam kompresi daripada dalam ketegangan.
Tes Cakram

Untuk bahan getas seperti keramik dan gelas, uji cakram telah dikembangkan, di mana cakram mengalami kompresi antara dua pelat datar. Ketika material dimuat seperti yang ditunjukkan, tegangan tarik berkembang tegak lurus terhadap garis tengah vertikal di sepanjang calram; fraktur dimulai dan piringan terbelah dua secara vertikal. Tegangan tarik 𝜎 dalam cakram seragam sepanjang garis tengah dan dapat dihitung dari rumus
𝜎 = 2P / (𝜋dt)
di mana P adalah beban saat patah, d adalah diameter piringan, dan t adalah ketebalannya. Untuk menghindari kegagalan prematur pada titik kontak, strip tipis logam lunak ditempatkan di antara piringan dan pelat. Strip ini juga melindungi pelat dari rusak selama pengujian. Fraktur di tengah spesimen telah digunakan dalam pembuatan tabung mulus.
Deformasi Geser
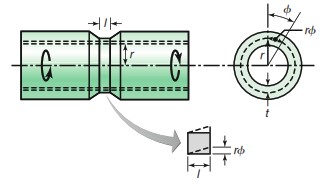
Selain mengalami beban tarik dan kompresi, benda kerja dapat mengalami untuk regangan geser, seperti pada pembuatan lubang pada lembaran logam dalam swaging dan dalam pemotongan logam. Metode pengujian umumnya digunakan untuk menentukan sifat bahan dalam gaya geser adalah uji torsi. Untuk mendapatkan tegangan yang kira-kira seragam dan distribusi regangan di sepanjang penampang, tes ini biasanya dilakukan pada spesimen tubular tipis.
Spesimen torsi biasanya memiliki bagian penampang tereduksi untuk membatasi deformasi menjadi sempit. Tegangan geser dapat dihitung dari rumus
𝜏 = T / (2𝜋r2t)
di mana T adalah torsi, r adalah jari-jari rata-rata dari tabung, dan t adalah tebal tabung pada titik bagian sempitnya. Regangan geser dapat dihitung dari rumus
𝛾 = r𝜙/l
di mana l adalah panjang tabung yang mengalami torsi dan 𝜙 sudut puntir dalam radian.
Rasio tegangan geser terhadap regangan geser dalam rentang elastis dikenal sebagai modulus geser, atau modulus kekakuan, G, besaran yang berhubungan dengan modulus elastisitas, E. Sudut puntir 𝜙 patah pada puntiran batang bundar padat pada kenaikan suhu juga berguna dalam memperkirakan forgeability (Kemampuan untuk ditempa) logam. Semakin besar jumlah tikungan sebelum kegagalan, semakin baik kemampuan untuk ditempa.
>> KLIK DI SINI UNTUK MEMBACA ARTIKEL SEPUTAR MATERIAL TEKNIK LAINNYA!
Kontributor: Daris Arsyada
Sumber:
Kalpakjian, Serope dan Schmid, Steven R. (2009). Manufacturing Engineering and Technology (6th ed). New Jersey: Prentice Hall.
Leave a Reply
Want to join the discussion?Feel free to contribute!